Tray erectors build and designs, wide ranges of trays, boxes that are tailored for customers’ demands. Tray erectors are used for making trays, by folding corrugated paperboards and applying adhesives on the corners. Stain retaining feature of tray erectors differentiates it from other packaging machinery. The high operational speed of tray erectors further extends its application in the market. Tray erectors are operator friendly, they provide easy loading and unloading of the blanks. They provide extra strength to the material by interlocking...
Monday, 26 March 2018
Four Side Seal Machine Market – Regional Markets, Technology, Types and Applications
Four side sealing technique is widely used for single-serve packaging applications in pouches, sachets, etc. The sealing process is carried out with the help of high-end automatic four side seal machines. The automatic four side seal machine is the latest technological development in the packaging machinery industry. The four side seal machine is cost-effective and offers convenience in the production process. The machine is operated through series of integrated PLC commands. It offers high seal integrity with minimal time change required to...
Pressure Sensitive Labels to Account for over 48% Revenue Share in Medical Device Labeling Market by 2025 End
According to the latest market report published by Transparency Market Research titled “Medical Device Labeling Market: Global Industry Analysis, Size, Share, Growth, Trends and Forecast, 2017–2025,” global revenues generated from sales of disposable consumables were around US$ 716.4 Mn in 2017, and are projected to increase at a CAGR of 6.3% during forecast period 2017-2025. Disposable consumables segment is anticipated to be the highest contributor to the global medical device labeling market, over the forecast period, 2017-2025.
The...
Underfill Materials Market Driven by Growing Demand for Portable Electronic Products
An up to date business and commerce publication by Transparency Market Research (TMR) has detected that the global underfill materials market is largely consolidated among a handful of players, and forecasted the competitive landscape to remain limited within the major players despite a few new entrants making a mark. The analyst of the TMR report has notified that as of 2017, Henkel and NAMICS Corporation were the two leading companies, accounting for more than half of the total shares in the global underfill materials, although H.B...
Industrial plastic bags Market – Regional Markets, Technology, Types and Applications
The global industrial plastic bags market is vastly driven by the development of food, pharmaceutical, electrical and electronics industries. To expand geographical outreach, manufacturers are focusing on product innovation and technological advancement by developing their products in packaging market. However, to overcome government stringent regulations manufacturers are focusing on bio-degradable plastic bags as these bags are easy to recycle and do not pose a threat to environment. The industrial plastic bags are mostly used for the transportation...
Rigid Paper Containers Market: Quantitative Market Analysis, Current and Future Trends
Growing awareness in people about the harm of plastics to nature has motivated people to use eco-friendly and biodegradable packaging. This has increased the production cost of the plastics as well as various restrictions on the production of plastics applied by governments across the globe. Replacing containers or paper canisters or composite cans are getting popular among consumers due to various advantages of it, including recyclable, biodegradable, low cost, high strength and much more. Rigid paper containers are not made up of paper only,...
Composite packs Market – Key Growth Boosters, Significant Trends & Opportunities
A composite pack, made up of multiple materials such as foam, plywood, plastics, polystyrene, timber, etc., could be used to provide ideal packaging solution for the goods in transit whether by road or air. It offers optimum strength and insulation properties to the material packed inside it. They are available in random shapes and sizes in pre-assembled or component form, depending upon the requirements of the customer. The composite packs, when used for packaging of fragile goods, reduce the rates of damage and offer safe delivery of the goods....
Collagen Market-By Source (Pig, Poultry, Cow, and Marine), By Product (Natural, Hydrolyzed and Gelatin), By Application (Cosmetics, Healthcare, Food and Beverage), and By Region-Forecast 2022-2031
SDKI Inc. published a new report on the collagen market on January 25, 2022. This study includes the statistical and analytical approaches ...
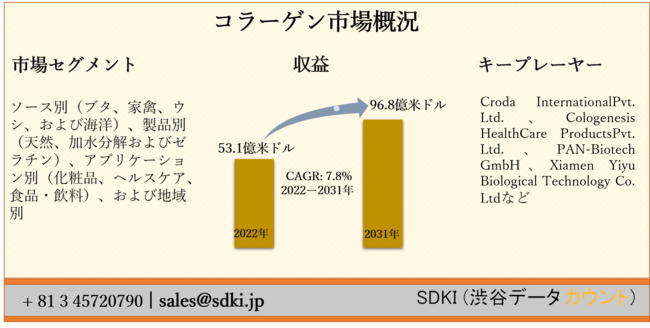